ROPA Euro Tiger 6S
Video Preview
Introduction
ROPA Tiger 6S - greatly improved efficiency paired with digital networking in the most powerful sugar-beet lifter worldwide from the leader in the market. ROPA adds the Tiger 6S to its range of self-propelled sugar-beet lifters. It will be in series production in time for the 2020 harvest. After several years of field testing, pilot models are already in operation in parts of Europe for the 2019 season. A new generation of extremely high-performance computers forms the telematics centre with predictive analytics, online diagnostics and partially autonomous sugar-beet harvesting. The Tiger 6S now occupies the premium segment in the market and with its advanced computer architecture it is considerably more than the technical and visual continuing development of the current Tiger 6.
A New Image
The new image of the ROPA Tiger 6S symbolises digitalisation and Agriculture 4.0. The light-blue line shows and represents the networking of the Tiger internally and externally with the R-Connect online portal. The new product logo is based on the smooth geometric shapes of the low poly style. The play of light and shadow gives the Tiger 6S even greater depth and dynamic. The striking colouring with dark-grey outside contours harmonises with the pale aluminium grey and bright yellow. The Tiger is designed for pride in ownership, to arouse emotion and at the same time to meet the promise of quality.
TWO ENGINE VARIANTS - WITH MEGA-TORQUE – EXTREMELY ECONOMICAL
Volvo Penta TWD1683VE with 796 hp/585 kW Volvo Penta has designed this engine specifically for operation in the Tiger 6S. With 16.12 litre capacity, common rail injection, SCR catalytic converter and AdBlue, this engine type delivers its energy even more efficiently and is much cleaner. This powerful package with its dual turbochargers generates a huge maximum torque of 3650 Nm. At only 1000 rpm it already generates 3550 Nm, enabling the machine to save fuel and lift beets longer in the low speed range. With its modern technology this diesel engine complies with EU V emission category even without exhaust gas recirculation. The basis for greater daily output at less fuel consumption and even more power at lower speeds. Volvo Penta TAD1643VE-B with 768 hp/565 kW With a capacity of 16.12 litres and pump-nozzle injection (PDE), the engine of Tiger 6Sa is the reliable and robust power package, that many customers already know and appreciate from Tiger 6a. This engine does not require AdBlue, SCR catalyst and exhaust gas recirculation. A powerful torque of 3,260 Nm is transmitted by the stepless traction drive at optimal efficiency. This engine will no longer be available in the EU from the year 2021 due to changes in legislation.
PANORAMA CABIN WITH IMPROVED, COMFORTABLE OPERATION AND TWO R-TOUCH DISPLAYS
In comparison with the predecessors, the Tiger 6S has two 12.1-inch operating terminals with high pixel density resulting in even sharper resolution. Operation at the terminal with interactive buttons is even more intuitive and uses the same logic as tablets and smartphones.
In addition to the machine functions, two separate video streams can also be shown on the R-Touch display on the left A-pillar.
R-CONNECT ONLINE PORTAL
R-Connect telematics module and remote diagnostics as standard equipment The ROPA Tiger 6S comes with the efficient telematics hardware including SIM card for online access as standard equipment. The telematics module is thus the basis for proactive Service 4.0, particularly for predictive analytics and fast assistance and diagnostics if service is required on any continent. If service work is required, the service technician can link directly to the terminal and the machine controller to assist the driver with resolving the problem.
R-TRIM - AUTOMATIC DEFOLIATOR HEIGHT ADJUSTMENT
At the Agritechnica in Hanover ROPA presented two new developments that automatically adjust the working depths of the harvesting attachment on the Tiger 6S: • R-Trim - automatic adjustment of the defoliator height • R-Contour - automatic share depth adjustment of the individual rows at the RR lifting unit Both systems adapt their working depth to the changing conditions in the beet crop throughout the field. The automatic systems react to different crown heights or to ground unevenness crosswise to the direction of travel. The currently used measuring system at the scalper has been extended by an additional measuring system for recording the ground contour directly at the beet rows. 1. Normal beets - middle crown height; 2. Large beets - high crown height; 3. Normal beets - middle crown height; 4. Small beets - low crown height; 5. Angle sensor; 6. Defined defoliator height
R-CONTOUR
Automatic share depth adjustment of the individual rows at the RR lifting unit
The driver uses the joystick on the operating console to set the lifting depth as required and thus defines how deep the lifter share will penetrate the soil. Ultrasonic sensors beside every beet row record the ground surface contour. A new, powerful on-board computer processes the measured values and ensures that the lifting depth is maintained in accordance with the ground contour. Compared to the previous systems for automatic adjustment of single rows, this system has many advantages, particularly with higher growth in beet rows beside lanes.
Slope compensation up to 10%
The automatic slope compensation via six hydraulic cylinders and sensors is also unique among 3-axle sugar beet harvesters. The chassis is kept completely horizontal for up to 10 percent side slope. The gravity centre and, thus, the load of the wheels on the slope bottom side are shifted to the slope top side.
Centre of gravity and soil pressure compensation
The track depth of the wheels on the slope bottom side is substantially reduced, the infiltration capacity is retained, thus significantly reducing erosion risk during heavy rains. The slope stability and traction increase greatly, the risk of tipping over is considerably reduced alongside with increased driving comfort.
R-BALANCE - HYDRAULIC CHASSIS WITH SLOPE COMPENSATION
On the slpe, the load and the gravity centre of the slope bottom side are shifted to the slope top side: this results in soil-protective sugar beet harvesting even on slopes.
Cabin
PANORAMIC VIEW
The cabin with improved, comfortable operation and two R-Touch displays
In comparison with the predecessors, the Tiger 6S has two 12.1-inch operating terminals with high pixel density resulting in even sharper resolution. Operation at the terminal with interactive buttons is even more intuitive and uses the same logic as tablets and smartphones.
In addition to the machine functions, two separate video streams can also be shown on the R-Touch display on the left A-pillar. The Tiger 6S has digital cameras as standard. The image quality of the digital cameras is significantly better, and an additional Ethernet network is integrated into the machine to handle the resulting greatly increased volumes of data.
High-tech machine with chassis for sustainable soil protection
Compared to the chassis on earlier 3-axle beet harvesters (with the central axle fixed to the frame), this reduces the sway of machine by one third! The reason for the improvement is the hydraulic connection of the cylinders at the front and rear axles on one side, so unevenness at one wheel at a different level only affects the frame by 33 per cent compared to the previous system. Thanks to the reduction of the chassis swing, the row and depth control are improved simultaneously, as the frame is averaged to the position of three axles.
DRIVER'S POSITION
Ergonomic control element
The unloading conveyor and the bunker unloading can be controlled even more conveniently from the new ergonomic control element on the left armrest.
Ergonomic joystick
Three function buttons on the right multifunction joystick can be programmed, e.g. for wide-area window wiper.
R-View in the R-Touch display
The relevant camera image is automatically displayed on the left R-Touch display while reversing or when unloading the bunker. The rear part of the machine is displayed on the monitor in the bird's eye view. Obstacles are visible and collisions are avoided.
COMFORT
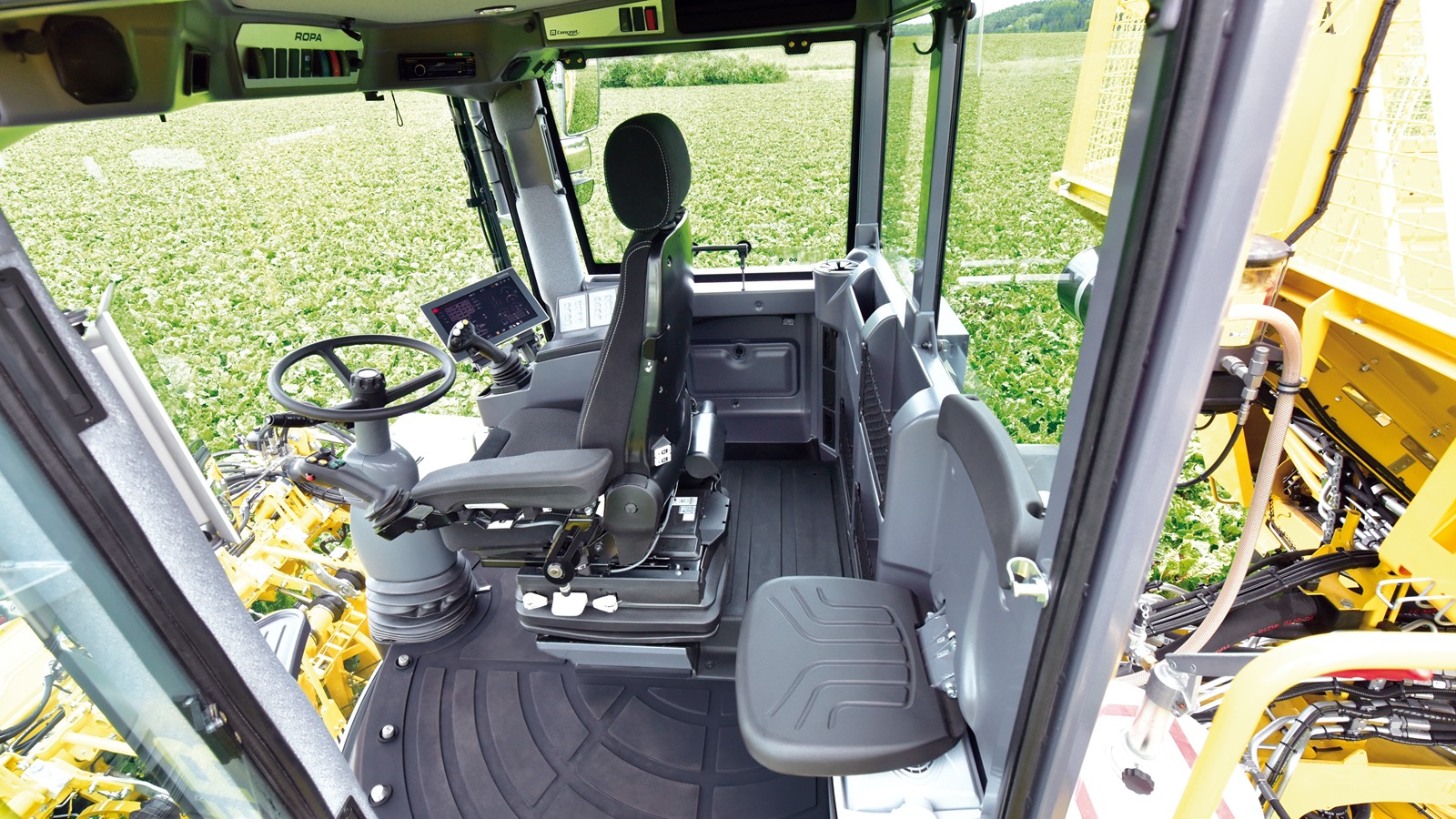
The driver is at the centre
Generously dimensioned shelves, storage compartments and plenty of space around the driver. A cooler and the integrated seat ventilation for hot days and seat heater for colder weather are standard equipment.
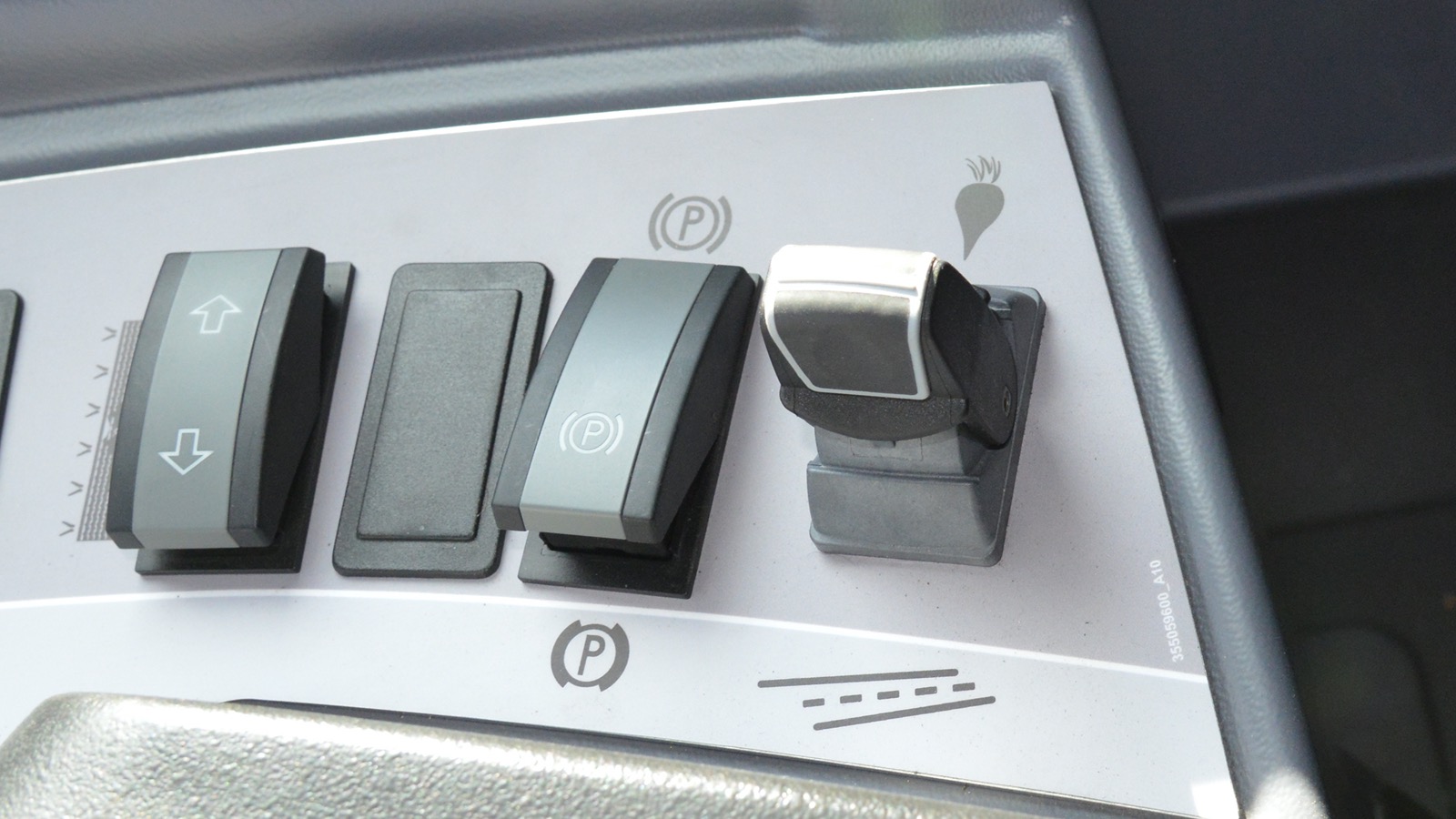
Automatic folding
The ROPA Tiger 6S switches automatically from road drive mode to field mode via a switch. Unloading conveyor, one metre wide ring elevator, bunker auger and other groups fold one by one, in some cases simultaneously. The sensor-controlled monitoring systems exclude operating errors and collisions. The entire folding process with simultaneous activation of all functions takes a very short time.
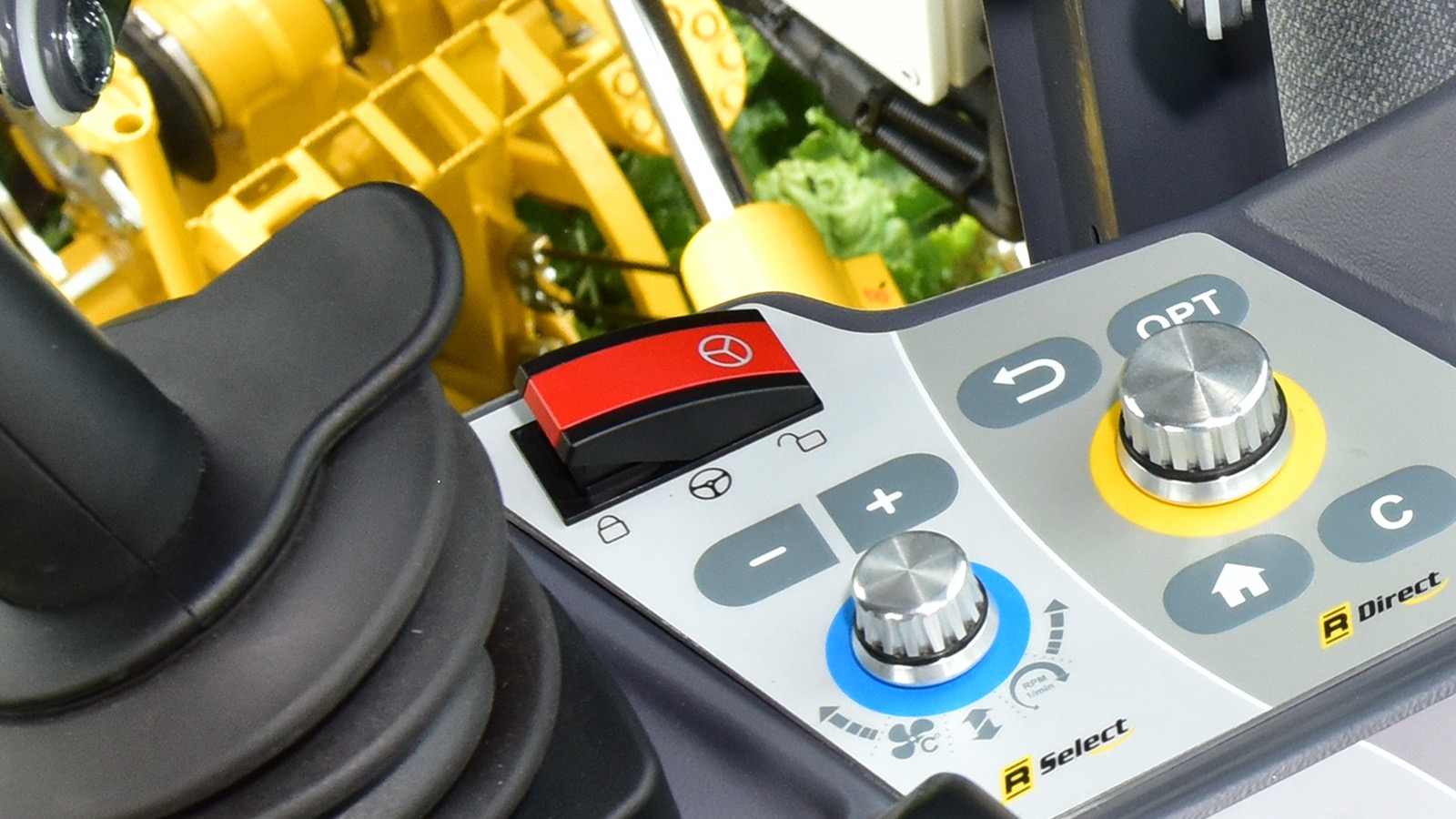
Main steering switch
The new "intelligent main steering switch" in red automatically synchronises the articulation and front-axle steering for travel on the road as well as straight-ahead positioning of the rear wheels.
18,600 LUMENS ON THE DRIVER'S CABIN
Powerful LED lights turn night to day
The Tiger 6S is fully equipped with LED spotlights with the combination of working spotlights and headlights providing outstanding illumination.
Lights menu
Individual or all working lights can be switched on with a finger on the touch terminal.
And again a one fingertip is enough to back up and recall three different lighting programs.
Operation
Intuitive operating concept of the ROPA Tiger 6S
In this video, Ole Thielmann gives a brief overview of the basic functions and diverse setting options of the ROPA Tiger 6S. It provides an additional support in the upcoming campaign.
Operation at the terminal with interactive buttons is even more intuitive and uses the same logic as tablets and smartphones. In comparison with the predecessors, the Tiger 6S has two 12.1-inch operating terminals with high pixel density resulting in even sharper resolution.In addition to the machine functions, two separate video streams from the digital cameras, installed as standard, can also be shown on the R-Touch display on the left A-pillar.
ROPA Tiger 6S - additional information, documents, and videos
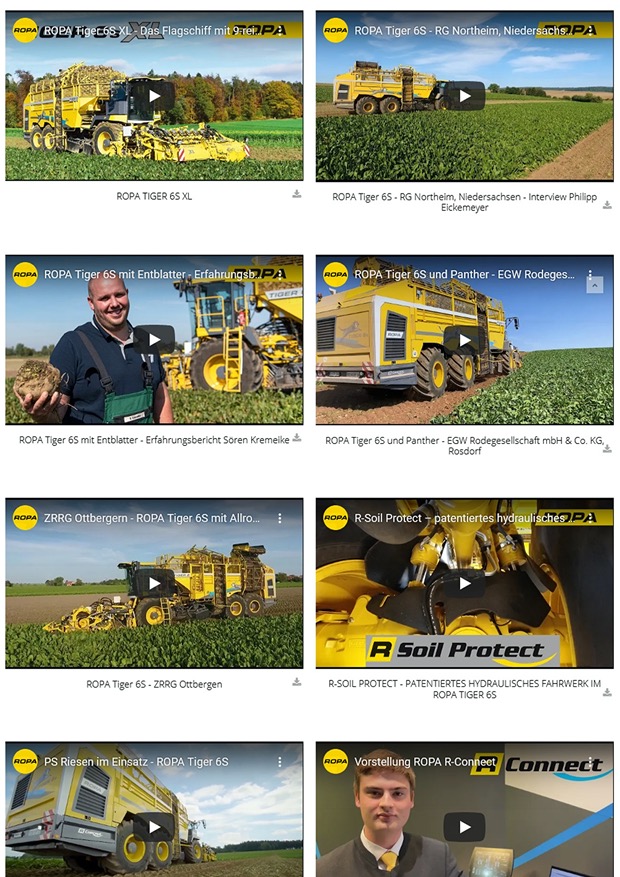
Additional videos on practical use of the Tiger 6S are available in the media centre
R-Connect
R-CONNECT ONLINE PORTAL
R-Connect telematics module and remote diagnostics as standard equipment
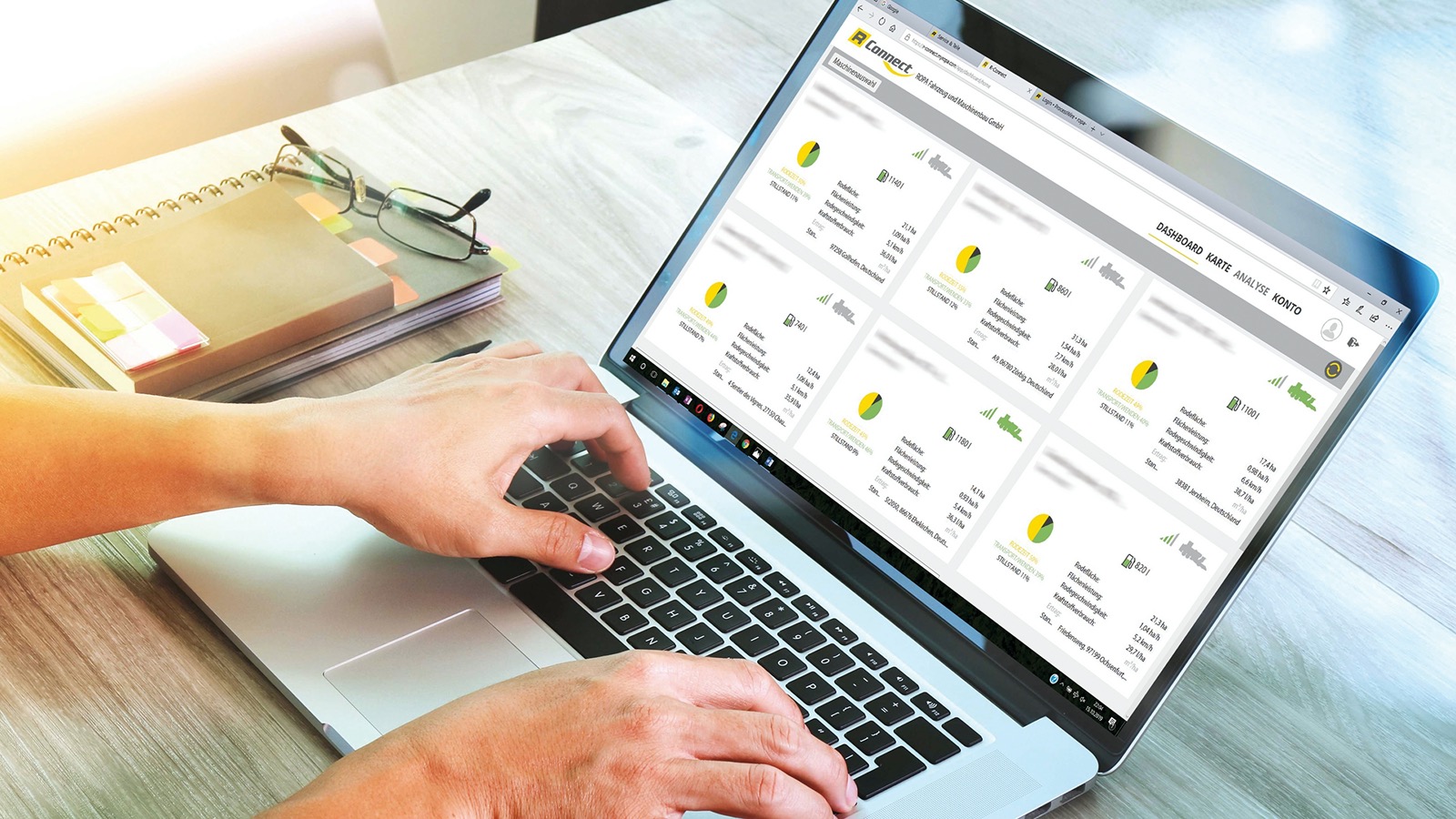
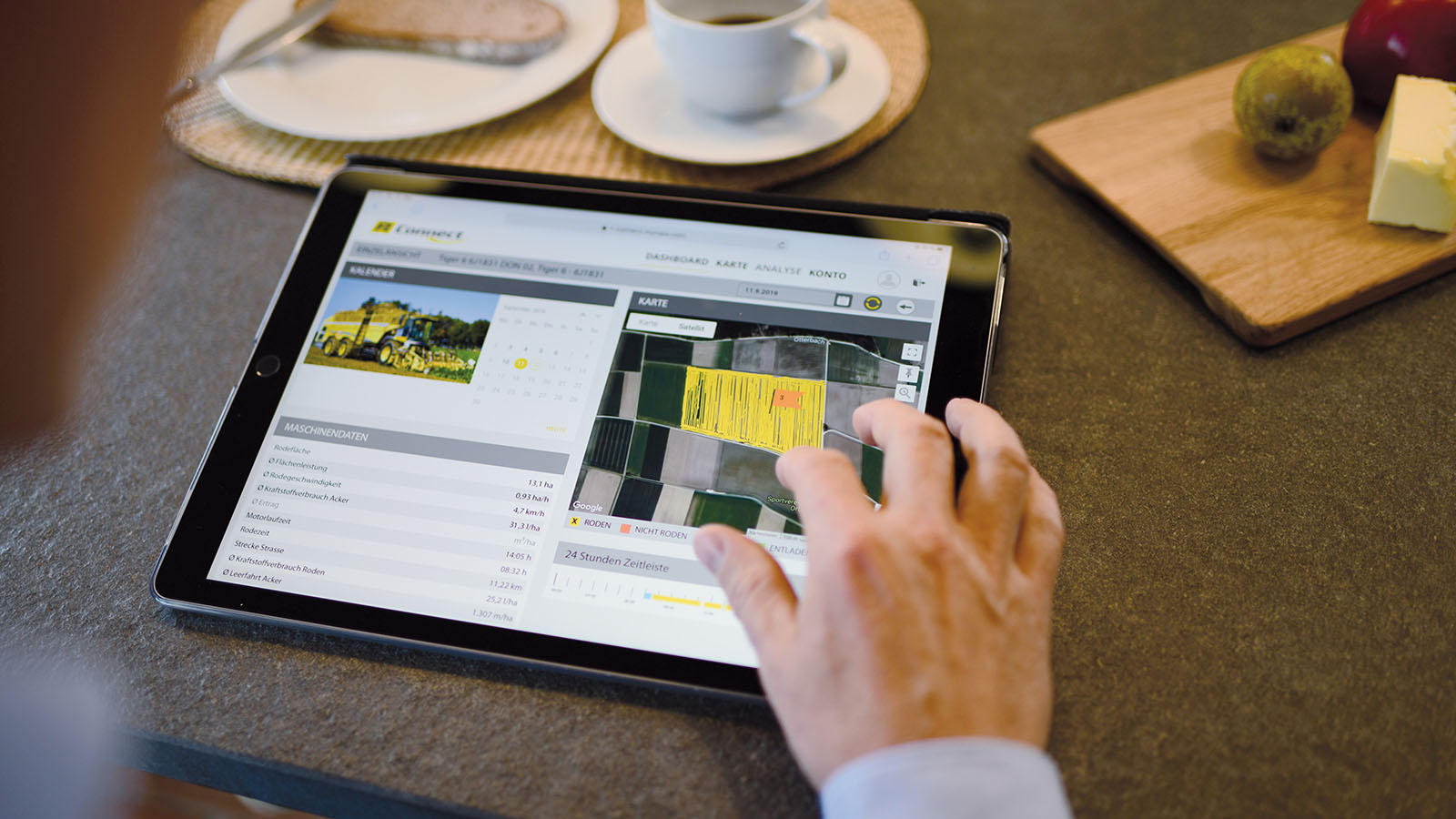
R-CONNECT - SIMPLY CONNECTED
Many things become much easier with the R-Connect
Many things become much easier with the R-Connect online portal, even if it's only about bringing a snack for the driver to the field.
Experience the numerous possibilities of ROPA R-Connect and talk to your ROPA company representative or sales partner.
R-CONNECT MONITOR - SILVER MEDAL AT AGRITECHNICA
R-Connect Monitor offers intelligent and fully automatic image documentation during the sugar beet harvest. Photos tagged with the location are automatically taken during lifting and while emptying the bunker. The pictures taken by the optional camera on the cabin roof for monitoring the state of the crop before harvest and the pictures of the camera on the unloading conveyor for checking the quality of the harvest during unloading are allocated to the lifting order in the R-Connect portal.
The harvested area, the yield (number of bunker fillings) and the position of the beet clamp can all be recorded. A visual record of the beet area before the harvest and also the result of the harvest can therefore be documented.
R-Connect monitor for image documentation
The harvested area, the yield (number of bunker fillings) and the position of the beet clamp can all be recorded. This Agritechnica innovation can now save a visual record of the beet area before the harvest and also the result of the harvest.
- Images tagged with location record.
- Documentation of the machine settings with the image.
- Photos tagged with the location are automatically taken during lifting and while emptying the bunker and allocated to the harvest order in the R-Connect portal.
INNOVATIONS AND NEW ITEMS AT AGRITECHNICA 2019
- Images showing the state of the beet crop before harvest in connection with the machine settings and position data
- Monitoring for weed abundance before lifting
- Monitoring the beet crop for diseases, such as rhizoctonia, cercospora and nematodes
- Optional additional manual image documentation if irregularities cause problems with lifting, e.g. water in the field, foreign objects, power poles, overseeding etc.
- Pictures during unloading for quality control and documentation of the result of the harvest
- The documentation of the extraneous matter on the ground and weeds in the beet clamp is very useful information for the logistics of transport with reference to the time required, capability of storage of the beets etc.
- Contractors and harvesting cooperatives can use the pictures to show customers as evidence of, for example, requirements for increased work (lifting costs)
- A wide range of sensor data such as rpm, speeds, pressing, volume measurements etc. is much more informative when it is linked with pictures!
R-CONNECT ONLINE SERVICE
Remote diagnostics, help and maintenance
At Agritechnica in Hanover, ROPA demonstrated the new Tiger 6S, which is networked with the R-Connect portal via the telematics module installed as standard. ROPA's R-Connect monitor has won a silver medal for the innovations at Agritechnica for fully automated image documentation during the sugar beet harvest.
Now the online service is focused on the further development of the R-Connect online portal.
If a driver needs an assistance in case of service, the R-Connect online service can be used to provide a remote support. In the future, the downtime can be reduced thanks to the new functions of predictive maintenance (predictive service).
R-Soil Protect
Hydraulic chassis system - roll stabilisation with load compensation, patented
ROPA has developed an innovative chassis concept with an oscillating front axle in conjunction with two hydraulically supported rear axles specially for the flagship Tiger. Compared to the chassis on previous 3-axle beet harvesters (with the central axle fixed to the frame), this reduces the sway of machine by one third! The reason for the improvement is the hydraulic connection of the cylinders at the front and rear axles on one side, so unevenness at one wheel at a different level only affects the frame by 33 per cent compared to the previous system. Thanks to the reduction of the chassis swing, the row and depth control are improved simultaneously, as the frame is averaged to the position of three axles. The hydraulic connection of the axles always distributes the load equally over all 6 wheels.
The hydraulic chassis system minimizes tyres load and ground pressure, thus ensuring further reduction of tyre inflation pressure.
ROPA R-Soil Protect
- Significantly improved soil protection due to tyre pressure reduced by 1 bar in comparison with euro-Tiger V8-4 - unique for harvesting root crops
- 49% greater tyre contact area, 33% lower contact pressure with the IF1000/55 R32 CerexBib
- Significant reduction of load peaks by load transfer: by 8 % less on the first axle, 37 % less on the second axle, 43 % less on the third axle
- Equal load distribution on all wheels by networked hydraulics
- On the slope, the load and the gravity center of the slope bottom side are shifted to the slope top side
- Cleaning elements are guided horizontally even on slopes, providing perfect cleaning performance
- Soil-protective sugar beet harvesting also on the side slope without additional tyres inflation pressure increase
- Maintaining and protection of soil structure, ensuring infiltration capacity and air exchange
SOIL-PROTECTIVE HYDRAULIC CHASSIS SYSTEM WITH ULTRAFLEX TYRE TECHNOLOGY
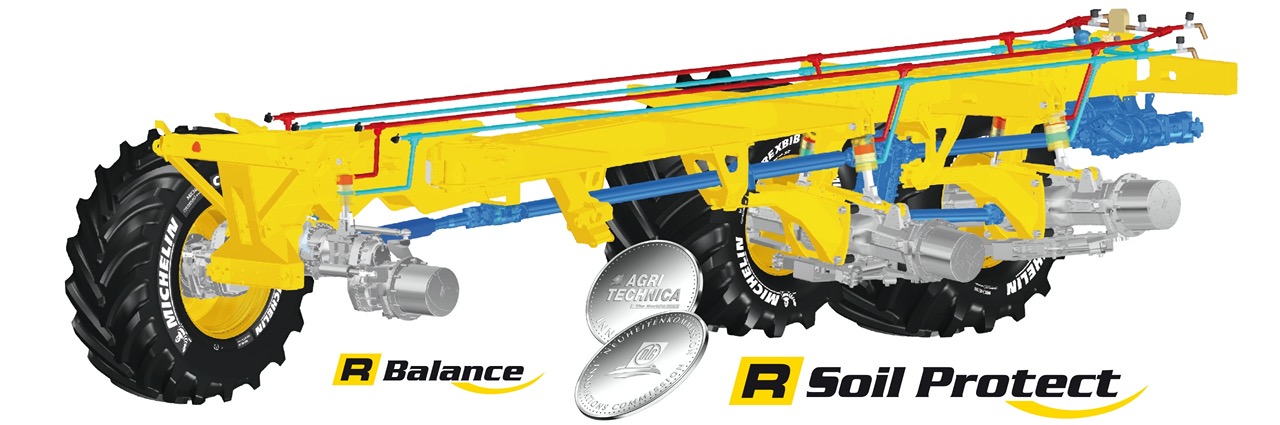
Low tyre inflation pressure for sustainable land management
ROPA R-Soil Protect is the combination of a soil-protective, hydraulic chassis system with MICHELIN CerexBib tyre technology.This soil protection concept was awarded a silver medal at Agritechnica in Hanover. It only requires 1.4 bar tyre pressure and it is available as an option in the Tiger 6S. The synergy of the load-balancing hydraulic chassis with the new generation of MICHELIN IF1000/55 R32 CerexBib tyres offers even more contact surface with sustained soil protection and significantly reduced contact pressure.
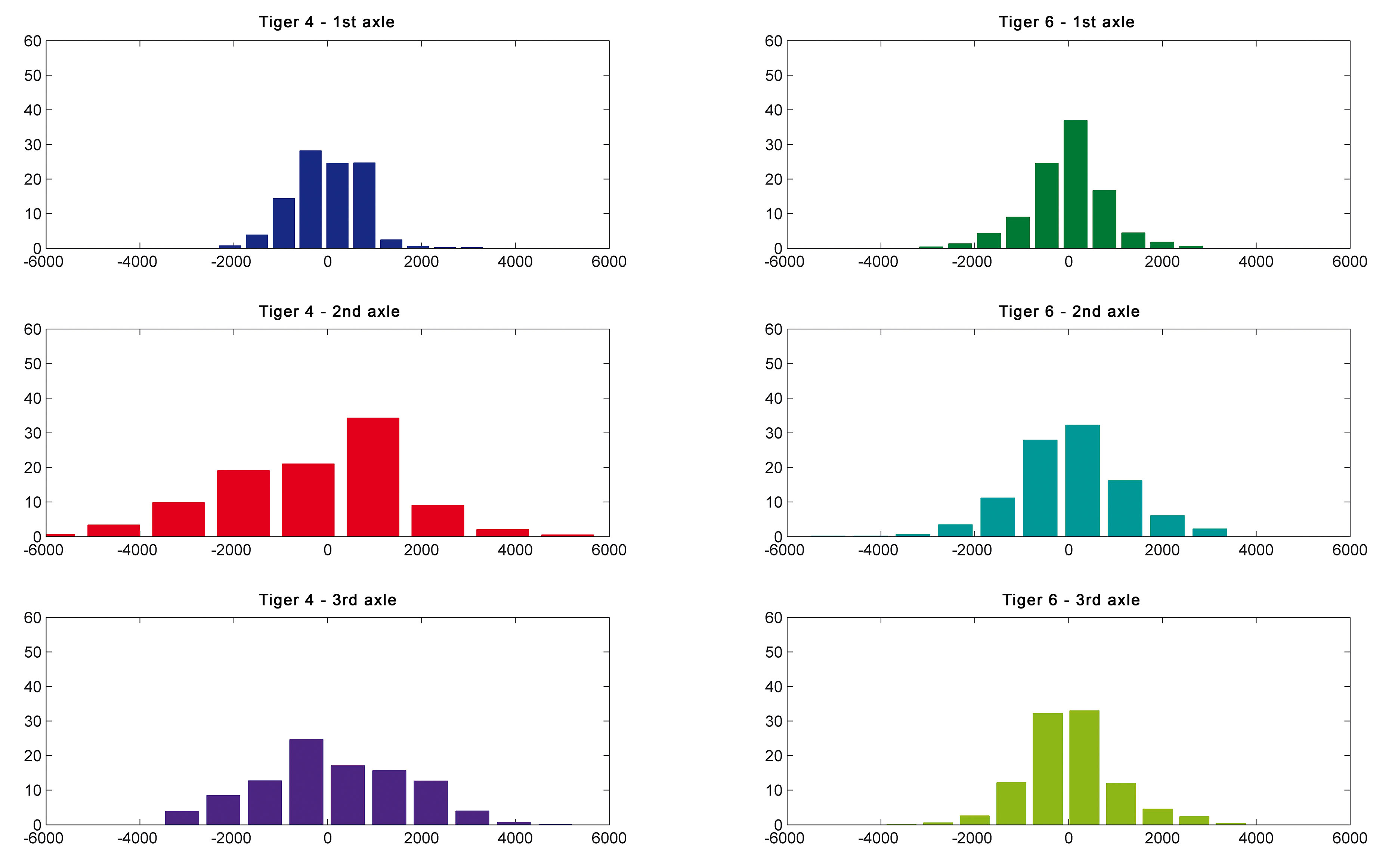
Increased soil protection with significantly reduced load peaks
The chassis of the Tiger 6 reduces the load peaks by
- 8% on the 1st axle
- 37% on the 2nd axle
- 43% on the 3rd axle
HYDRAULIC CHASSIS SYSTEM
Slope compensation up to 10%
The automatic slope compensation via six hydraulic cylinders and sensors is also unique among 3-axle sugar beet harvesters. The chassis is kept completely horizontal for up to 10 percent side slope. The gravity centre and, thus, the load of the wheels on the slope bottom side are shifted to the slope top side.
Centre of gravity and soil pressure compensation
The track depth of the wheels on the slope bottom side is substantially reduced, the infiltration capacity is retained, thus significantly reducing erosion risk during heavy rains. The slope stability and traction increase greatly, the risk of tipping over is considerably reduced alongside with increased driving comfort.
STEPLESS CVR GEARBOX FOR EFFICIENT POWER TRANSFER
Direct power transmission with cardan shafts ensures even traction at all wheels with very high torque
As a unique selling proposition on the market of 3-axle sugar beet harvesters, the Tiger has a direct power transmission via directly linear situated cardan shafts from traction drive to both rear axles and front axle, which is a great advantage for better traction in changing or difficult soil and harvesting conditions. Thanks to hydraulic chassis the load is always distributed evenly.
Stepless CVR gearbox for efficient power transfer
The new stepless traction drive was specifically developed by ROPA, Omsi and Bosch-Rexroth for the ROPA Tiger with its high drive power. The "constant variable ROPA" gearbox (CVR) consists of three hydraulic motors on a compound gearbox and is located between the engine compartment and the third axle. The maximum speed of 40 km/h can be reached by the Tiger 6S at an extremely economical 1,200 rpm. Harvesting in the field requires an engine speed of only 1,100 rpm. Depending on power requirements the rotational speed of the Tiger is automatically regulated up to 1,650 rpm. The multi-disk differential brakes integrated into the axles (protected from dirt) running in oil bath "tame" the Tiger as required.
Harvesting Technology
SEMI-AUTONOMOUS HARVESTING
ROPA presented two new developments that automatically adjust the working depths of the harvesting attachment on the Tiger 6S:
- R-Trim - automatic adjustment of the defoliator height
- R-Contour - automatic share depth adjustment of the individual rows at the RR lifting unit
Both systems adapt their working depth to the changing conditions in the beet crop throughout the field. The automatic systems react to different crown heights or to ground unevenness crosswise to the direction of travel. The currently used measuring system at the scalper has been extended by an additional measuring system for recording the ground contour directly at the beet rows.
R-TRIM - AUTOMATIC DEFOLIATOR HEIGHT ADJUSTMENT
Automatic defoliator height adjustment and ground contour sensor system for better quality of the harvested beets combined with a significant ease of operation
A new powerful on-board computer on the lifting unit of the Tiger 6S reads all measured values within a split second and, with the aid of the newly developed software, changes the defoliator height or the lifting depth of the individual rows. The combination and interaction of both systems significantly relieve the driver, which allows partly autonomous guiding of the lifter attachment. Topping losses due to changes in the condition of the crop are avoided without stress for the driver despite the reduction in the size of cut-off leaf stalks. This prevents not only the unnecessary pickup of soil by the lifting share and increased fuel consumption due to excessively deep lifting, but also root fracture of the beet if harvesting too flat.
The Micro-Topper comb detects the crown height of the topped beets. A height profile (blue line in the chart) is calculated from the average values of these crown heights. The height of the defoliator shaft is constantly adjusted to this profile. This prevents too intensive topping of the beet crowns, e.g. when the beet crop changes from small to large. Furthermore, too large leaf stalks are avoided when the beet size changes from large to small.
How does it work?
The driver sets in the menu the desired height of the defoliator shaft over the cutting height of the scalper flail (red arrow in the chart). This setting defines the average length of the stalks remaining on the beet after the defoliator knives. An angle sensor on each Micro-Topper records the crown height of each beet row. In the case of differences in the crop growth (e.g. dry areas) the activated R-Trim automatically corrects the height guide of the defoliator shaft depending on the highest beet.
R-CONTOUR
Automatic share depth adjustment of the individual rows at the RR lifting unit
The machine operator uses the joystick on the operating console to set the lifting depth as required and thus defines how deep the lifter share will penetrate the soil. Ultrasonic sensors beside every beet row record the ground surface contour. Powerful on-board computers process the measured values and ensure that the lifting depth is maintained in accordance with the ground contour. Compared to the previous systems for automatic adjustment of single rows, this system has many advantages, particularly with higher growth in beet rows beside lanes.
How does it work?
The driver activates the R-Contour (ground contour sensor system) in the terminal. Thus, the share depth adapts to the ground contours. The activated R-Contour prevents root fracture of the beet if harvesting too flat or unnecessary pickup of soil if harvesting too deep. The share depth adjustment is displayed synchronously on the terminal.
AUTOMATIC SHARE DEPTH ADJUSTMENT FOR UNEVEN GROUND CONTOUR, ULTRASONIC SENSORS BESIDE EVERY BEET ROW RECORD THE GROUND SURFACE CONTOUR
RR LIFTING UNIT
RR lifting unit with automatic share depth adjustment of the individual rows and hydraulic stone protection
The RR lifting unit is equipped with counter-rotating oscillating shares, seven lifting rollers, completely maintenance-free hydraulic stone protection and single-row adjustment of the share depth. The 850 mm large depth-control wheels combined with the intelligent three-point suspension guarantee accurate depth control of the lifter. Maintenance costs are minimised with adjustable taper roller bearings in transmissions and the oscillating share drive.
With seven lifting rollers, welded as standard with extremely abrasion-resistant, carbide containing hard-coated wire "Ropa Screwtec". Simple, fast exchange of the lifting rollers for varying conditions (different diameters, outfeed, infeed, etc.)
CONVENIENT MAINTENANCE POSITION
Maintenance position
The defoliator and the lifter assembly can be raised hydraulically up to 90° above the lifting unit for service (scalper flails, lifting shares). It is raised from the cabin by pressing a button without requiring the driver to leave the cabin, or from the ground using the push buttons.
Start engine
The diesel engine can be started and switched off by pushing a button on the lifter.
DEFOLIATOR UNIT
RAS - ROPA all-round defoliator
Integral leaf-layer or leaf ejector
The integral leaf layer shreds the beet leaves and deposits them between the rows. A press of the button in the cabin switches the machine between topping modes. When operating with leaf ejection the shredded beet leaves are spread over the harvested area by a leaf-spreader with a leaf auger feeding the leaves to it. Optionally, it can be equipped with RBSO (without switch-over function to integral) with 4 fixed depth-control wheels as well as with a leaf pile conveyor for harvesting beet leaves (biogas or dairy cattle).
RIS/RISU - ROPA integral defoliator
ROPA integral defoliator - standard model for normal harvesting conditions
Leaves from the beet crowns are mulched with robust defoliator knives and spread between the rows. This process spreads the beet leaves with all their nutrients evenly over the soil, forming the optimal basis for the subsequent cultivation for quick conversion of the green waste to humus. The integral defoliator is available with depth-control wheels (RISU) and mechanically folding leaf sensor or without depth-control wheels (RISU) with a hydraulically folding leaf sensor.
MICRO-TOPPER
The comb of the Micro-Topper follows each beet head, adjusting the trimming gap to the size of the head, so that the beet is cut not too much and returns maximum yield. The intensity of the cut can be easily adjusted from the cabin. You may choose between topping and "shaving off" leaves only (micro-topping).
RUBBER-DEFOLIATOR
RES - ROPA rubber defoliator
The speed and height of the two fully hydraulically powered and counter-rotating cleaning rotors can be independently adjusted – unique! The front shaft as a combined shaft is fitted with steel blades and cleaning rubbers, the second defoliator shaft is fitted with cleaning rubbers only.
Various settings can be stored and accessed on the joystick using a memory function.
CLEANING
Offset strainer wheel tines
Agitator at the transition to the second strainer wheel (optional)
Cleaner on elevator rubber
Rotating transition tubes at the elevator infeed prevent accumulation of soil
View from above
Rotating transition tubes at the elevator infeed prevent accumulation of soil
View from below
Cleaning - gentle, efficient and individually adjustable
The hydraulically tensioned sieve conveyor efficiently transports the beets to the first strainer wheel. The portal axis enable maximum throughput without slowing the beet flow or damaging the beets. The driver can steplessly adjust the sieve conveyor speed and reverse it if necessary from the cabin. The beet flow monitoring prevents the beets from overflowing the machine. Three strainer wheels equipped with forged tines, which have improved speed adjustment (a separate pressure sensor for each strainer wheel), clean the beets with extreme efficiency and care. The offset carrier tines ensure fast forwarding even at low strainer wheel rotation speeds.
BUNKER
43 m³ large beet bunker
The automatic bunker filling allows optimum traction under all harvest conditions by excellent weight distribution.
Yield indicator using ultrasound sensors
Two ultrasound sensors measure the load by totalling the bunker loads and save it in the order database.
UNLOADING CONVEYOR
The extra-long unloading conveyor is attached high up.
A great advantage when loading trailers driving alongside, because the transfer is closer to horizontal. The unloading conveyor is 3-way foldable and 2000 mm wide for simple laying of 10-metre-wide piles or easy loading on trailers. Gentle polyurethane fingers guarantee high feeding capacity with short unloading times of less than 50 sec. with a full beet bunker holding approx. 43 m³.
Ergonomic control element
Fast truck loading, gentle and convenient bunker unloading. Control element on the left armrest for fine control of bunker unloading.
Engine
VOLVO PENTA - TWO ENGINE VARIANTS
Power package with mega torque – extreme economy
The Volvo Penta Stage V D16 off-road engine offers ROPA sugar beet harvesters high performance and reliability.
Michael Gruber (sugar beet technology area manager at ROPA Fahrzeug- und Maschinenbau GmbH) in the interview with Volvo Penta.
VOLVO PENTA TWD1683VE WITH 796 HP/585 KW
Engine Tiger 6Sd
Volvo Penta has designed this engine specifically for operation in the Tiger 6S. With 16.12 litre capacity, common rail injection, SCR catalytic converter and AdBlue, this engine type delivers its energy even more efficiently and is much cleaner.
This powerful package with its dual turbochargers generates a huge maximum torque of 3650 Nm. At only 1000 rpm it already generates 3550 Nm, enabling the machine to save fuel and lift beets longer in the low speed range. With its modern technology this diesel engine complies with EU V emission category even without exhaust gas recirculation.
The basis for greater daily output at less fuel consumption and even more power at lower speeds.
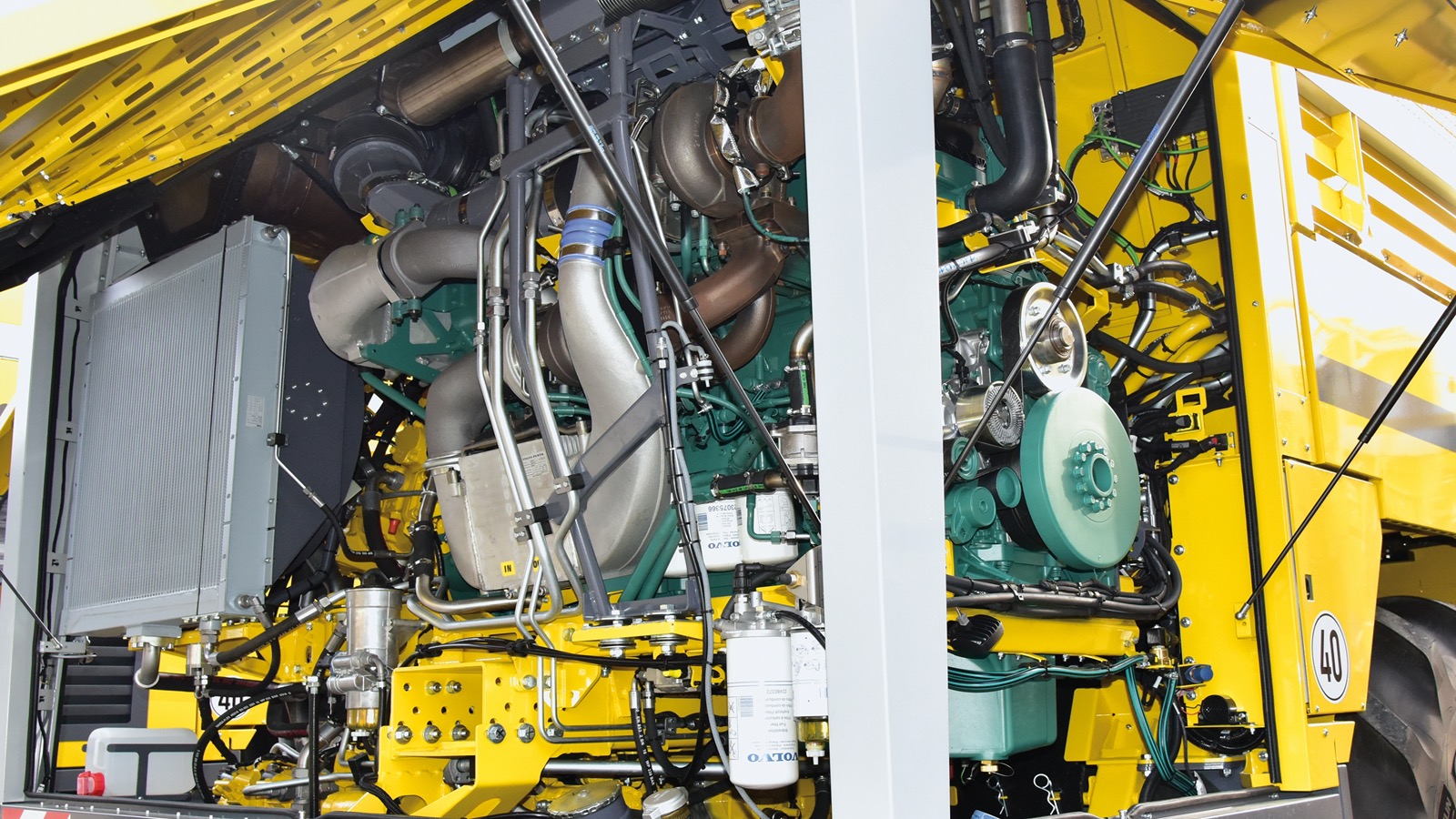
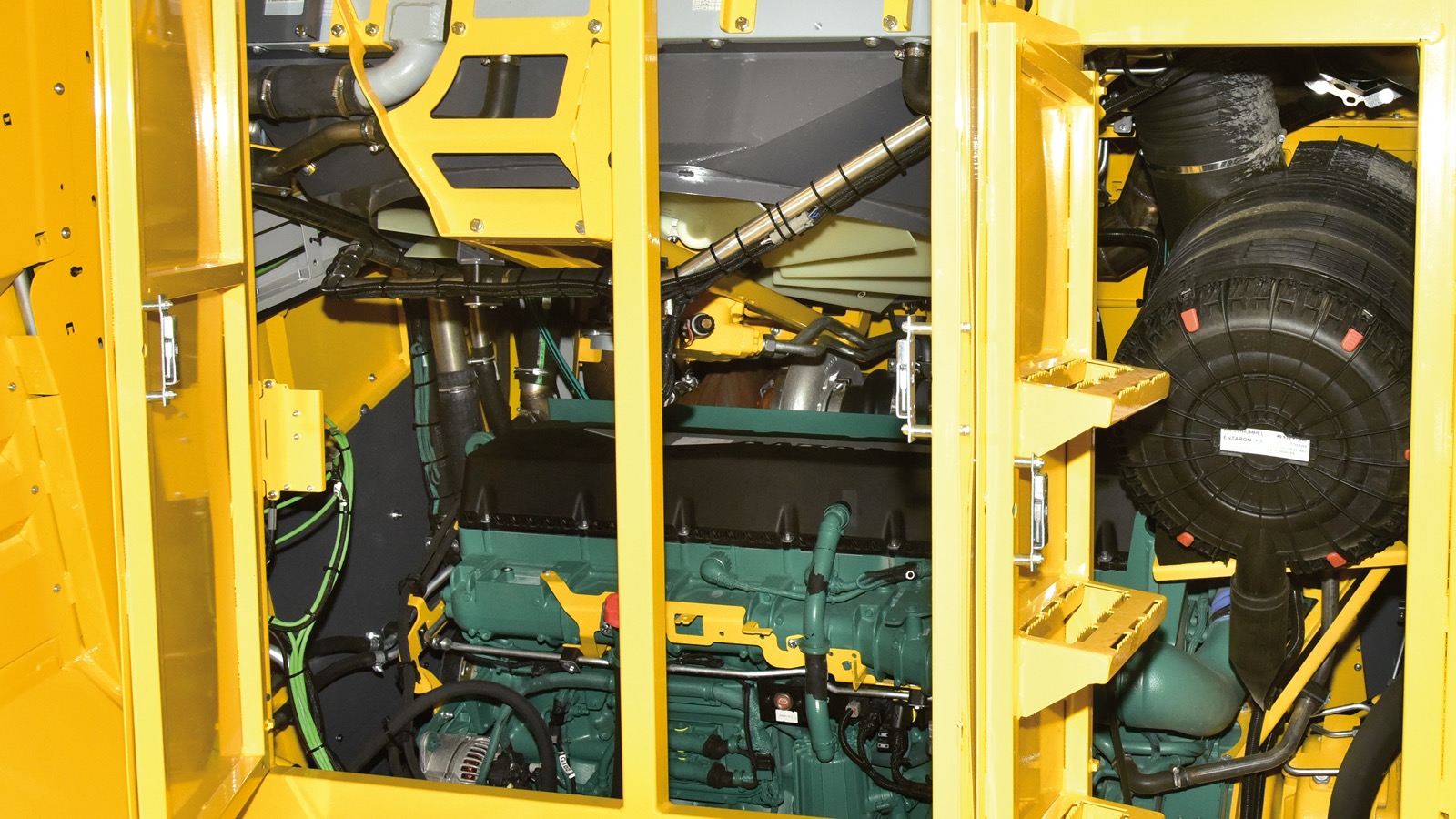
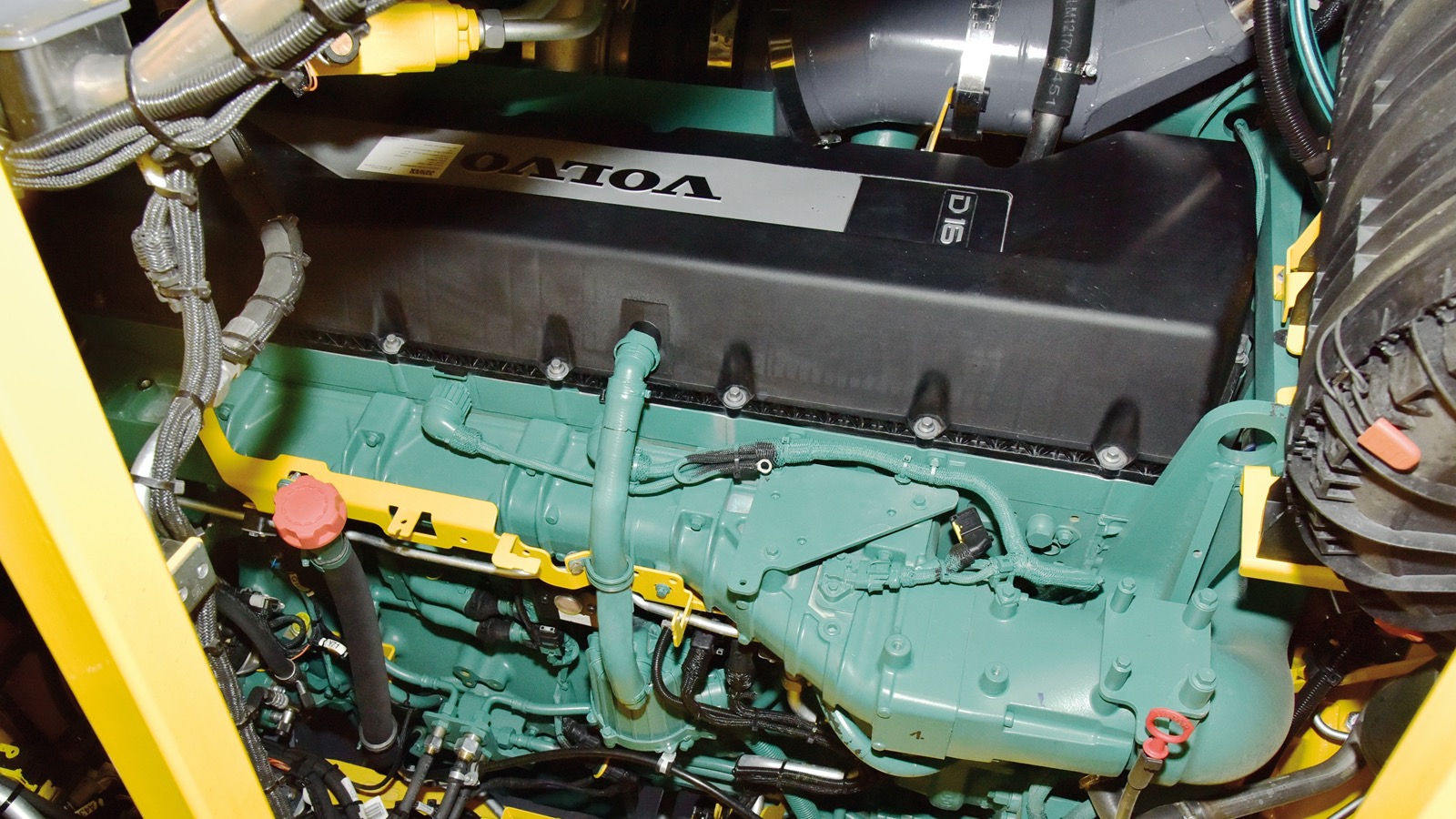
VOLVO PENTA TAD1643VE-B WITH 768 HP/565 KW
Engine Tiger 6Sa
With a capacity of 16.12 litres and pump-nozzle injection (PDE), the engine of Tiger 6Sa is the reliable and robust power package, that many customers already know and appreciate from Tiger 6a. This engine does not require AdBlue, SCR catalyst and exhaust gas recirculation. A powerful torque of 3,260 Nm is transmitted by the stepless traction drive at optimal efficiency. This engine will no longer be available in the EU from the year 2021 due to changes in legislation.
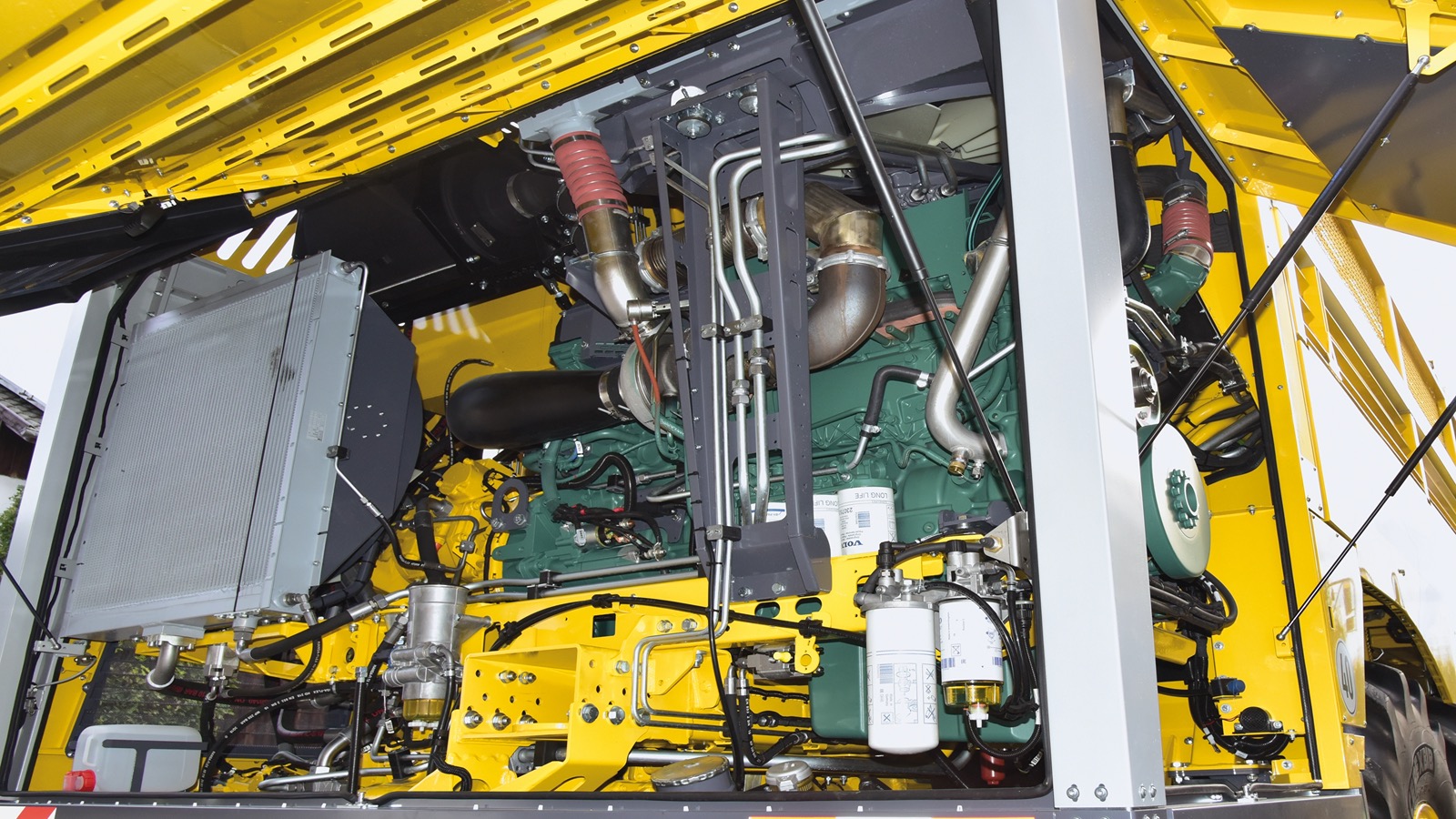
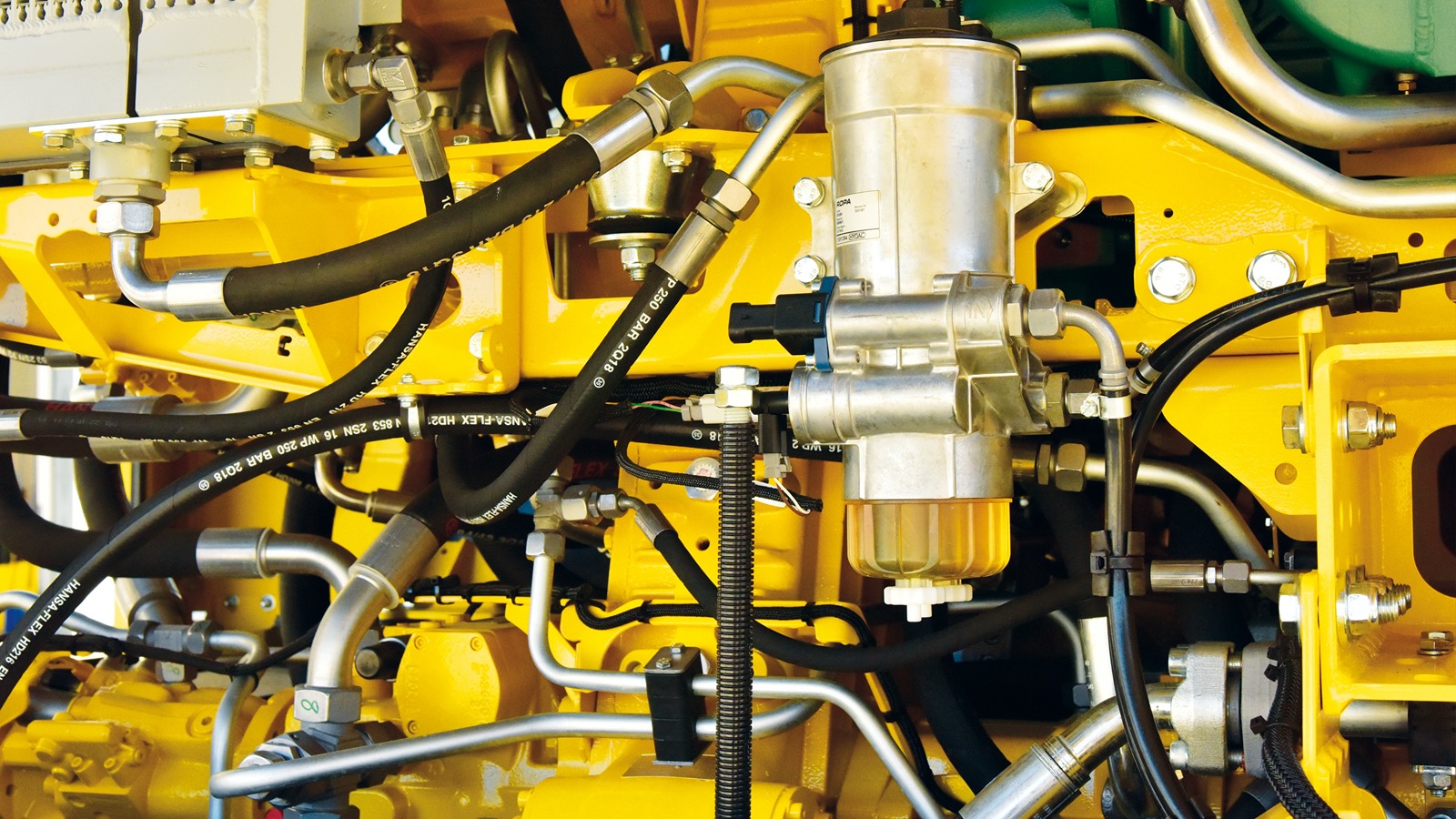
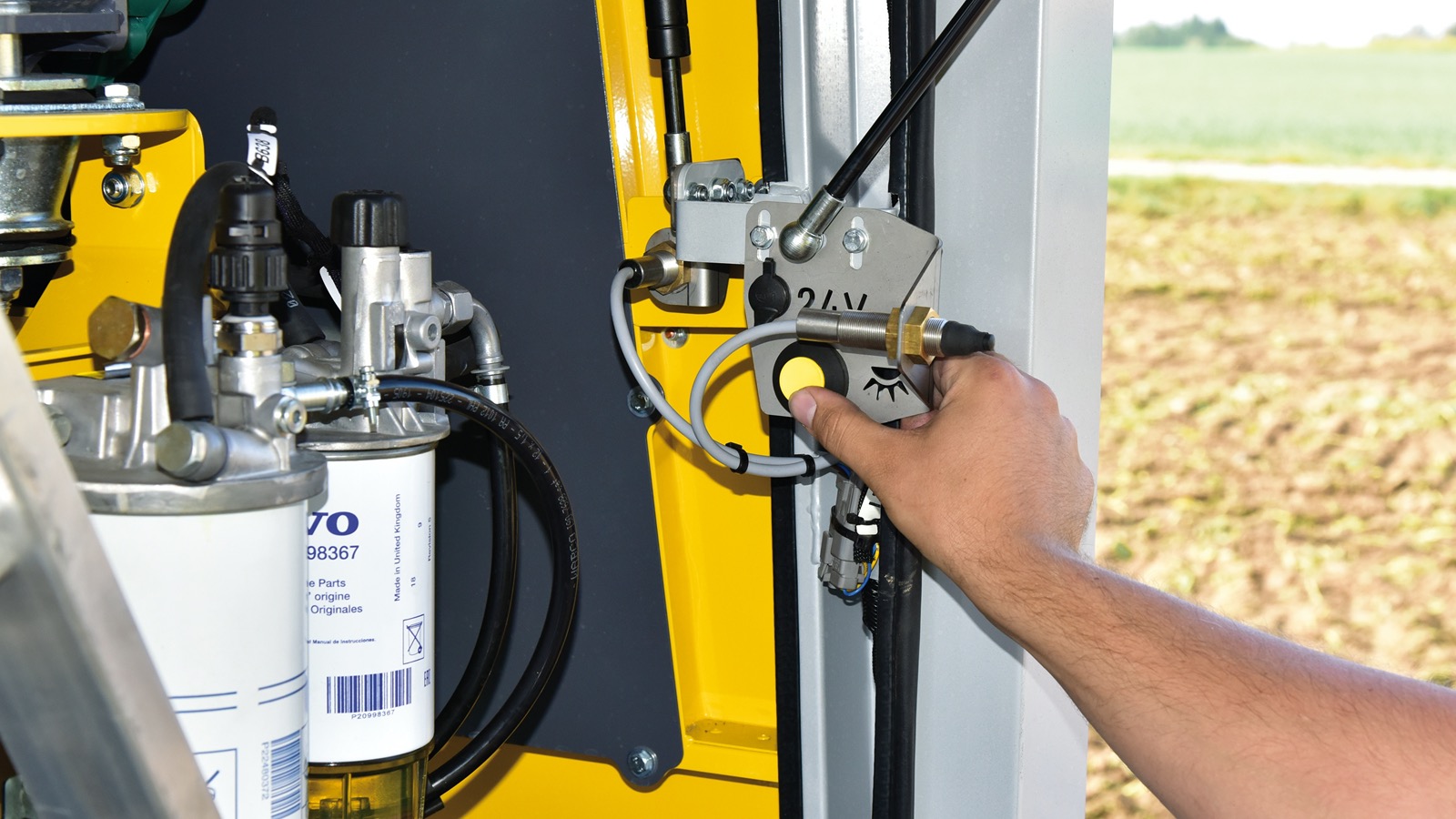
Tiger 6S XL
Extra Wide Harvesting Units
The ROPA Tiger 6S equipped with 8- or 9-row wide harvesting units of the RR-XL series is capable of covering significantly larger areas at reduced harvesting speed. Advantages of this version are reduced fuel consumption, lower fixed costs and an improved topping quality. With the wide RR-XL lifting units the front axle of the Tiger 6S can use even wider Michelin IF 900/60 R38 CerexBib2 tyres for greater soil protection. Less passes and manoeuvres also contribute to soil protection.
SIGNIFICANTLY GREATER AREA COVERED
Significantly higher area performance with reduced fuel consumption leads to lower costs during the profitable and efficient sugar beet harvesting season. Fewer passes and manoeuvres also contribute to better soil protection.
Technical Data
Dimensions
Length
14.99 m
Height
4.00 m (transport position)
Width
3.00 m (6 rows with 45 cm rows)
3.30 m (6-rows at 50 cm width and 45-50 cm variable)
< 3.30 m (with RR-XL depending on the size of the lifting unit)
Unladen weight
from 33,400 kg, depending on equipment
Bunker capacity
over 43 m³ / 30 t
Diesel engine - 2 engine models available
VOLVO PENTA TWD1683VE
796 hp/585 kW
16.12 l displacement
Volvo Penta 6-cylinder inline engine
Common rail injection
Emission level EU 5, USA TIER 4f, with SCR catalytic converter and AdBlue, maximum fuel sulphur content 15 ppm required to meet exhaust emission standard
Max. torque 3,650 Nm, 3,550 Nm from as low as 1,000 rpm, working speed 1,100 rpm, automotive up to max. 1,650 rpm
VOLVO PENTA TAD1643VE-B
565 kW (768 hp)
16.12 l displacement
Volvo Penta 6-cylinder inline engine
Pump-nozzle injection (PNI)
WITHOUT AdBlue, WITHOUT exhaust gas recirculation
Fuel with sulphur content to max. 5,000 ppm permitted
Max. torque 3,260 Nm, working speed 1,100 rpm, automotive up to max. 1,650 rpm
not for USA and Canada
Fuel tank
1,320 l diesel
Fuel consumption displayed in l/ha and l/h in terminal
AdBlue tank
145 l AdBlue
(Volvo Penta TWD1683VE - 796 hp / 585 kW only)
Cooling system
Features
Flat side-by-side arrangement of cooling elements for charge air and water
Hinged CVR oil cooler and air conditioning system condenser
Dirt-resistant positioning of the radiator at rear top
Hydraulic oil cooler with open fan
Hydrostatically continuously driven and automatically reversible fan
Traction drive
Gears
Traction drive with stepless CVR gearbox for efficient power traction
Consisting of three hydraulic motors on the compound gearbox
Features
Continuous from 0 to 40 km/h without interruption (no gear change or switching)
40 km/h in road mode at 1,200 rpm, 17.5 km/h in the field at 1,240 rpm
Tyres
1st axle
Michelin CerexBib2 IF 800/70 R38 (1.4 bar)
2nd and 3rd axle
Michelin MegaXBib 1050/50 R32 (1.9 bar)
Optional
Michelin CerexBib 1000/55 R32 (1.4 bar)
Features
large tyre contact surface protects soil and allows high operating reliability even in wet conditions and on slopes
Chassis - R-Soil Protect
Features
Patented chassis design with oscillating front axle in conjunction with 2 hydraulically supported rear axles
Slope adaptation - R-Balance
Features
The chassis can be inclined by 10% to the slope on each side by 6 hydraulic cylinders
Automatic slope compensation by a 3-axis gyroscope with acceleration measurement for centrifugal force compensation (optional)
Chassis roll stabilisation
Roll stabilisation by hydraulic compensation of the oil level in the stabilisation cylinders on one side of the vehicle
Hydraulics
Pump distributor gears
With pressure circulation lubrication and gear oil cooler
Traction drive
Bosch Rexroth traction drive
Operating hydraulics
Well dimensioned load-sensing working hydraulic system by Bosch Rexroth, Bucher and Hydac
Cabin
Driver's position
Sound-insulated and tinted all-round windows with low horizon
Quiet stepless fan in heating and ventilation system (automatic climate control)
Grammer air-spring-mounted ROPA Evolution comfort seat with heating and active ventilation
Autopilot
Cruise control
console for telephone
AM/FM/CD/USB/Bluetooth/DAB+ Radio with external microphone for hands-free communication
14 litre cool box
Operation
R-Touch
Multifunctional joystick right with programmable keys
Bunker control element with joystick grip on the left armrest
Terminal
12.1“ R-Touch display on the operating console
12.1“ R-Touch display on the left A-pillar
Fully integrated machine diagnosis including DM1 error messages from the diesel engine in plain text
Lighting
2 LED interior lights
Window wipers
Wide-area window wiper
Camera
The relevant camera image is automatically displayed on the left R-Touch display while reversing or when unloading the bunker.
Defoliator/rubber defoliator
RIS
Integral defoliator unit with leaf spreading between beet rows
2 depth-control wheels
RISU
Integral defoliator unit with leaf spreading between beet rows
without depth-control wheels
RAS
All-round defoliator unit, push-button operation from the driver’s seat, can be changed for either integral topping or leaf ejection to left
2 depth-control wheels (optionally 4 depth-control wheels)
RBSO
Defoliator with side leaf ejection to the left
Leaf auger and leaf spreader
4 rigid depth-control wheels
Only available in 45 cm
(Only permitted in certain countries due to legislation)
RES
Rubber defoliator with leaf spreading between beet rows
2 depth-control wheels
Lifting unit
RR lifting unit
6, 8 or 9 rows
45 cm, 50 cm or variable (6-row only)
hydraulic share depth adjustment of the individual rows
hydraulic stone protection
85 cm depth-control wheels
7 lifting rollers
Fast stepless oscillating share drive by axial-piston motor
Adjustable taper roller bearings in oscillating share drive and lifting gears
Excellent view of lifting unit and scalper with no additional cameras
Maintenance position
Allows the defoliator and the lifting group to be raised 90 degrees for simple inspection and service of defoliator knives, scalper knife and lifting shares
Cleaning
Infeed conveyor
800 mm wide
50 mm pitch
1st strainer wheel
1,740 mm diameter
Strainer wheel with forged tines
6 offset strainer wheel tines
2nd and 3rd strainer wheels
1,500 mm diameter
Strainer wheels with forged tines
4 offset tines each strainer wheel
Guide grids
Height independently adjustable at 1st, 2nd, 3rd strainer wheel can be independently adjusted
guide grids can be replaced with spring tines segment by segment
Elevator
1,000 mm wide
Electrical system
Vehicle power supply
24 volt
Generator
150 A
Outlets
12 V socket on seat console, 1 pc.
24 V socket on seat console, 1 pc.
USB double socket 5V / 3.6A (USB-A and USB-B), 2 pcs.
Features
CAN-bus computer system with integrated diagnosis of all components connected to the terminal
Software can be updated at USB port
Lighting
Headlights
2 Hella C140 LED main headlights at the front on the defoliator unit
6 LED working headlights (1,700 lumen) Hella LED Oval 90 on the cabin roof
23 LED working floodlights (1,800 lumen) Nordic Lights
4 LED spotlights for lighting the engine compartment
Rotating beacons
Hella RotaLED Compact
Features
Coming-home function
Unloading conveyor
Features
Triple-fold conveyor for even easier establishment of 10-metre-wide clamps
Gentle PU fingers for high output and short unloading times
The speed of both conveyors is steplessly adjustable
Long conveyor with speed switch
Unloading conveyor width
200 cm for even easier unloading to trailer
Bunker unloading
in less than one minute
Overloading height
up to 4.00 m
Yield indicator
Features
Bunker contents are measured with 2 ultrasonic sensors
The total bunker loads (including partly loaded) are automatically recorded in the database
Equipment
Standard equipment
central lubricating system
Fuel consumption measurement
automatic climate control
1 digital camera as rear view camera
1 digital camera for strainer wheels unit
R-Connect telematics module incl. SIM card
Hard-coated scalper flails
Lifting rollers with a hard welded-on finish
Cleaner on elevator rubber
40 km/h
Manual slope compensation R-Balance
Other equipment options
Automatic slope compensation R-Balance
R-Contour (automatic share depth adjustment of single rows by ground contour detection)
R-Trim (automatic defoliator height adjustment)
Reinforced defoliator plate for integral defoliator
Defoliator with combined shaft instead of standard defoliator shaft
Leaf spreader in stone protection mode
Leaf pile equipment (only at defoliators with leaf ejection)
Inflow sheet with skid on scalper
Widia forged lifting shares
Data printer
R-Transfer PROFESSIONAL
R-Transfer BASIC
R-View video system (bird's-eye view)
1 digital camera for infeed conveyor
1 digital camera for unload conveyor
1 digital camera for beet crop on cabin roof
R-Connect Monitor
Non-slip speed measurement
2 LED high-beam headlamps (4,200 lumen each) on mirror brackets
4 LED high-beam headlamps (4,500 lumen each) on mirror brackets
Strainer wheel segments optionally with guide grids or spring tines on strainer wheels 1-3
Agitator in the 2nd strainer wheel
2nd strainer wheel discharge grid in standard, stone protection or spring tine model
Limit sensor on diesel tank
Additional chassis (required in Germany)
Reduction of maximum speed from 40 km/h to 32 km/h
Chicory equipment
Contour marking package